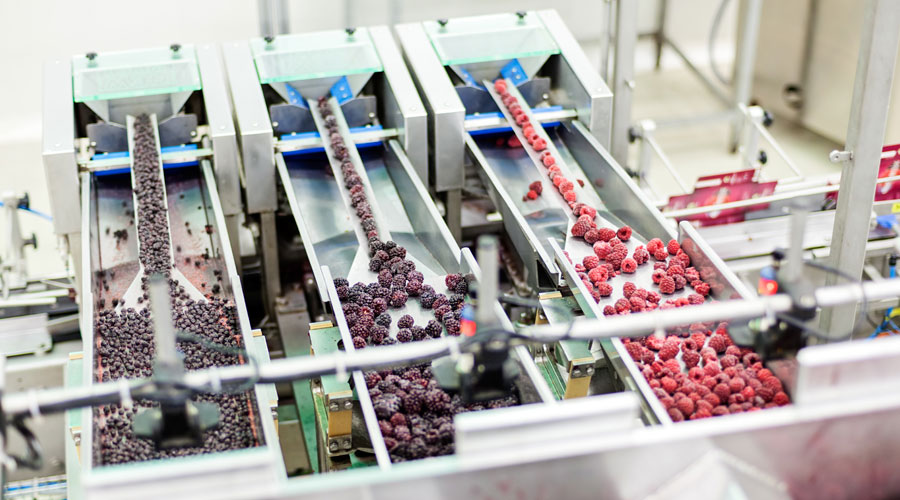
Making a Plan for Product Recalls
As a manufacturer, your customers expect you to have safe and reliable products. You may do everything in your power to ensure your goods are fit for sale, but exposures such as design flaws, manufacturing defects, inadequate warnings and unclear instructions can all negatively affect product safety. In the event that one of your products harms a customer or stakeholder, they may sue your business, possibly leading to costly legal fees and settlements. What’s more, following a product issue, your company must take corrective actions to curb losses and preserve its reputation. This may include carrying out a product recall, which is a complex process.
Product Recalls
In general, a product recall refers to the act of returning, exchanging or replacing a product in the marketplace after a defect is discovered. These defects can be anything that hinders a product’s performance, harms consumers or creates potential legal ramifications. For instance, the Canada Consumer Product Safety Act regulates consumer products and can demand a recall of certain items that might pose a danger to human health. Depending on the product type, there may be other legislation to adhere to, so it’s always wise to seek legal counsel in the event of manufacturing concerns.
Additionally, it’s important to be prepared with a plan that allows your company to mobilize quickly following a product recall. Consider the following tips for making a plan:
- Designate and delegate. The plan should assign employees to specific duties so that everyone knows their responsibilities in the event of a recall.
- Keep track of production. The plan should account for accurate recordkeeping. This makes it easier for your company to locate and recall defective goods quickly.
- Use feedback. The plan should allow you to monitor customer complaints and use feedback to flag problematic products.
- Spread the word. The plan should include a public relations strategy. You should have detailed plans in place for who will notify the public, how they will do it and when.
- Adapt and improve. The plan should allow you to reflect on how it was implemented and make improvements as needed.
- Consider compliance. Ensure your plan accounts for all applicable regulations and industry standards.
While having a plan in place for responding to product issues is important, it’s equally crucial to prevent future product issues whenever possible. Continual improvement should be a constant goal, and you should review your company’s communication plan, risk assessment procedures, recall strategy and similar activities on a regular basis.
For further protection, the right insurance policy can be invaluable. For instance, product liability coverage can help protect your company from a variety of liability concerns, even if a defect is caused by an outside supplier.
For more details on managing your cost of risk as a manufacturer, manufacturing insurance policy options, or to find out how to reduce your insurance costs call CMB at 780.424.2727 or click here to get a quote.